
- Source: heatmasters.net
Steel’s tensile strength can jump by 50% with proper metal heat treatment. This major improvement shows why heat treatment processes are vital in modern manufacturing.
Heat treatment affects industries of all types. Transportation, energy, defense, and manufacturing rely heavily on this process. Metal heat treating changes material properties like hardness, strength, and machinability through precise heating and cooling at temperatures up to 2400°F. The surface becomes harder while the core stays soft, which lets components absorb stress without cracking.
In this piece, we’ll look at why quality heat treatment remains essential in manufacturing. We’ll also explore the real costs of poor processes and see how new technology changes this vital industrial process.
The True Cost of Poor Heat Treatment
When manufacturing processes go wrong, the consequences can be far-reaching and expensive. Many of these issues can be traced back to one critical factor—how materials are treated during production. Without proper oversight, these missteps can result in equipment failures, safety hazards, and significant financial losses.
1. Production Line Failures and Downtime
Metal heat treatment is crucial to preventing unexpected tool and die failures that can bring manufacturing lines to a halt. Bad heat treatment that leads to early part failures can waste hundreds of production hours spent making tooling components. Safety-critical parts like seat belt mechanisms, aircraft engine components, and firearms assemblies could fail catastrophically if they don’t get proper thermal processing.
2. Warranty Claims and Brand Damage
Poor heat treatment creates problems beyond just production losses. Defective parts that reach customers force manufacturers to deal with expensive recalls, heavy financial penalties, and possible deadly accidents. A real-world example shows what it all means – a crankshaft gear that failed because of bad heat treatment caused a fatal aircraft crash and led to major legal battles.
3. Resource Wastage Statistics 2023
Research shows that only 10% of heat treatment problems come from the actual process. The biggest problems start earlier:
- Metal production quality issues
- Wrong original mechanical treatment choices
- Bad component design decisions
Specialized industries feel these financial effects strongly. Tool and die manufacturers can lose hundreds of production hours from just a few hours of wrong heat treatment. Companies lose millions in production dollars each year when parts fail early due to inadequate metal heat treatment.
Manufacturers need strong quality control systems to cut these losses. Quality control programs that track and study incoming materials have become standard practice. Modern heat treating equipment now comes with built-in monitoring controls to prevent expensive mistakes.
Quality Standards in Metal Heat Treating
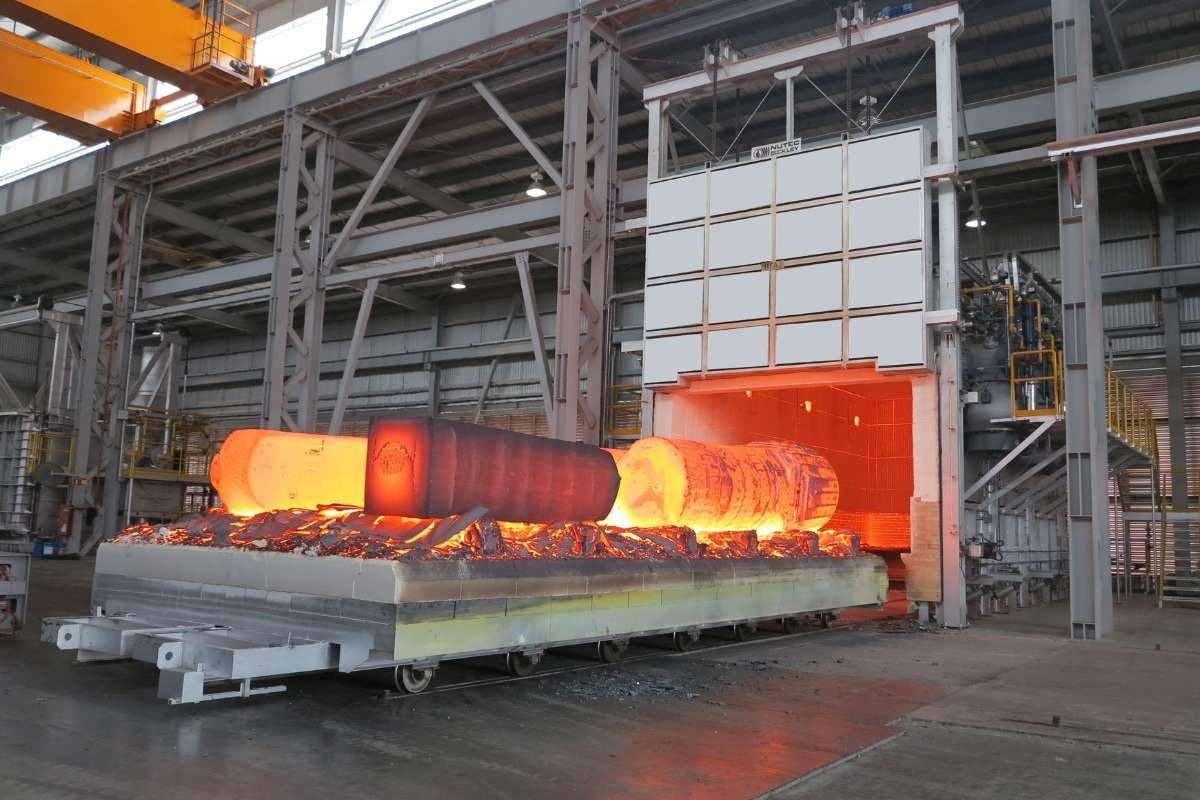
1. ISO 9001 Requirements
ISO 9001:2015 certification forms the foundation of quality management for heat treatment operations. The standard focuses on two key areas: meeting customer requirements and lining up with organizational strategy. The certification requires:
- Management and process controls
- Documentation and data storage protocols
- Continuous measurement and analysis of performance
- Implementation of corrective and preventive actions
Manufacturers can develop their own process-specific procedures, but they must validate all products and services strictly.
2. Industry-Specific Certifications
Specialized certifications go beyond ISO 9001 to meet unique industry requirements. The Automotive Industry Action Group’s CQI-9 Heat Treat System Assessment is the life-blood of automotive production. This complete process audit has:
A. Process Control Requirements:
- Detailed specifications for carburizing, nitriding, and induction hardening
- Equipment calibration and maintenance protocols
- Temperature and atmosphere monitoring systems
B. Quality Management Components:
- Supplier requirements and auditing procedures
- Personnel training and competency verification
- Documentation of process parameters
Aerospace companies follow AMS2750F standards that require precise temperature uniformity and control. Field test instruments must be calibrated every three months under this certification. AS9100D certification handles specific aerospace quality requirements and ensures consistent heat treatment results for critical components.
These standards bring clear benefits. Companies with proper certifications see better process control, fewer defects, and stronger customer trust. Heat treatment facilities must run intensive training programs so operators understand both equipment operation and basic metallurgical principles.
Certified facilities involved in metal heat treatment keep detailed records of every process step, from contract review to final inspection. Each job gets a full evaluation through test pieces, monitoring systems, and final quality certifications.
Modern Heat Treatment Technology
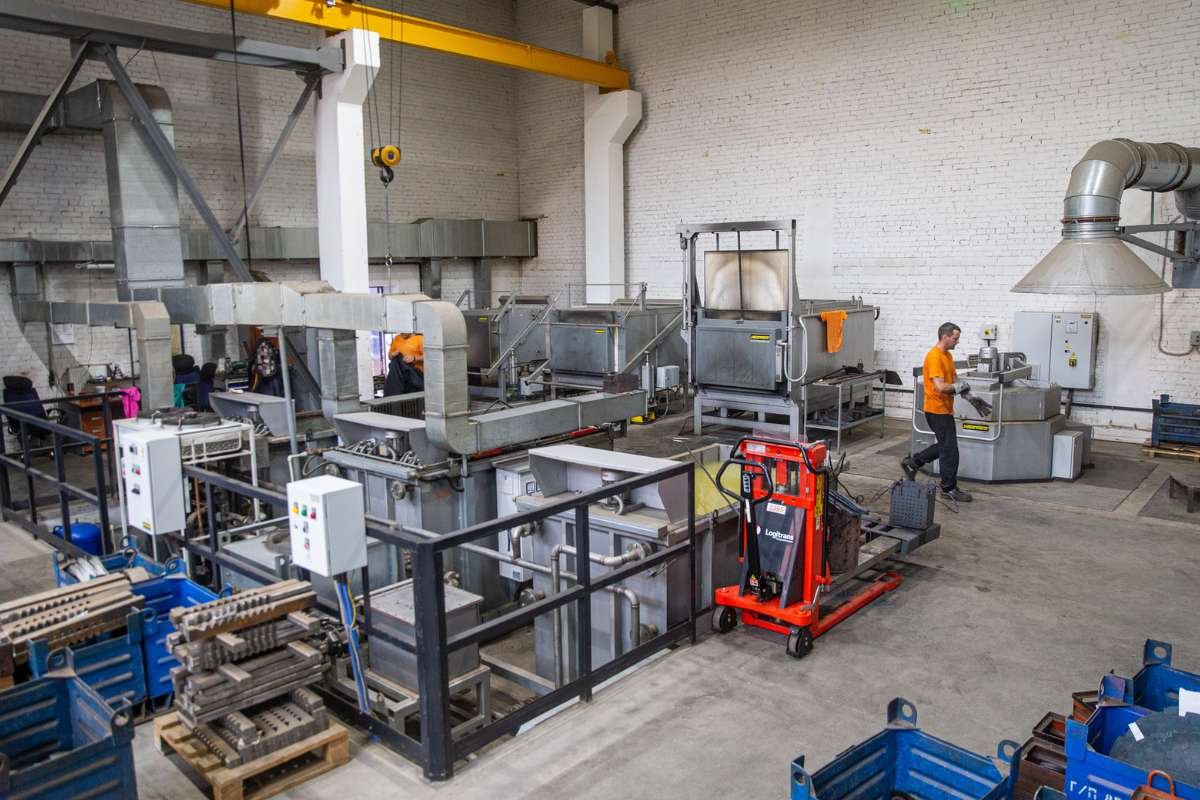
1. AI-Powered Temperature Control
Artificial intelligence now provides immediate monitoring of furnace conditions. This ensures optimal temperature control throughout the heating cycle. These systems detect problems instantly and allow quick adjustments without disrupting production. Furnaces maintain precise temperature uniformity through machine learning algorithms that minimize defects and enhance product quality.
Modern AI systems perform several vital tasks:
- Monitor free oxygen levels in burners of all sizes to maintain perfect ratios
- Track thermal stasis achievement
- Analyze gas consumption patterns
- Suggest cycle modifications to optimize performance
One of the most effective methods for achieving precise and uniform heating in industrial applications is induction heat treating. This technique uses electromagnetic fields to generate heat within the material itself, providing fast, energy-efficient, and localized heating. When combined with AI-powered monitoring systems, induction heat treating ensures consistent temperature control.
2. Real-Time Quality Monitoring
Modern metal heat treatment facilities use sophisticated monitoring systems that continuously analyze data. These systems give complete temperature profiling capabilities up to 1050°C (1922°F). Operators can track multiple parameters at once:
- Temperature uniformity across products
- Atmosphere composition in treatment chambers
- Cooling rates during quenching processes
Smart sensors combined with advanced analytics have reduced product defects. These improvements come from predictive rather than preventive maintenance.
3. Digital Twin Integration
Digital twin technology marks a significant advancement in heat treatment process control. This innovative system works with AI to optimize furnace operations. It also studies the best combinations of heating parameters.
The technology brings several important benefits:
- Reduces energy consumption through exact control
- Allows virtual testing of process modifications
- Gives immediate simulation of heat treatment processes
- Aids quick fault detection and diagnosis
A newer study, published in by manufacturers shows digital twins helped reduce component sizes while keeping performance standards high. To cite an instance, see how one implementation cut costs by 15% through optimized design.
These technological advances have transformed metal heat treatment into a highly controlled, evidence-based process. Manufacturers now achieve unprecedented precision levels while cutting operational costs and improving product quality.
ROI of Quality Heat Treatment

1. Extended Product Lifespan
Quality heat treatment changes material properties at a basic level. This leads to much better component durability. Manufacturers use precise temperature control to get the best mechanical properties. These changes help products last longer.
The process brings several key benefits:
- Better wear resistance by changing surface properties
- Higher resistance to corrosion and fatigue
- Improved mechanical properties that cut production costs
Metal heat treatment extends the service life of steel parts, resulting in fewer replacements over time, which is significant. Bad heat treatment can make tools useless. You lose your entire investment – raw materials, machining costs, and labor.
2. Reduced Maintenance Costs
Professional metal heat treatment facilities offer significant cost benefits through expert knowledge and quick operations. These advantages manifest in various ways:
Professional heat treaters keep costs down by:
- Paying 2-3 times less for gas or electricity
- Running furnaces non-stop without wasteful warm-up cycles
- Smart load management that keeps furnaces full
The commercial facilities have skilled experts who know the latest tech and rules. Their expertise cuts down costly mistakes and wasted materials.
Modern furnaces can pay for themselves by cutting outsourcing costs for manufacturers who think over in-house heat treatment. The real value goes beyond just saving money – proper heat treatment shows the true worth of the treated part.
Companies can boost their heat treatment ROI through smart lot sizing and planning. To cite an instance, mixing similar jobs without losing quality saves lots of money. Running costs at commercial heat treatment places are 50% lower than in-house options. This makes professional heat treatment an economical choice for many manufacturers.
Conclusion
Metal heat treatment is more than just a routine step in metal manufacturing—it’s a critical factor that determines the strength, durability, and reliability of industrial components. Poor heat treatment can lead to catastrophic failures, costly recalls, and wasted resources, while precision in thermal processing helps manufacturers maintain efficiency, reduce costs, and extend the lifespan of essential parts.
Companies that prioritize high-quality heat treatment will continue to gain a competitive edge, ensuring stronger, safer, and more cost-effective products for the industries that rely on them.